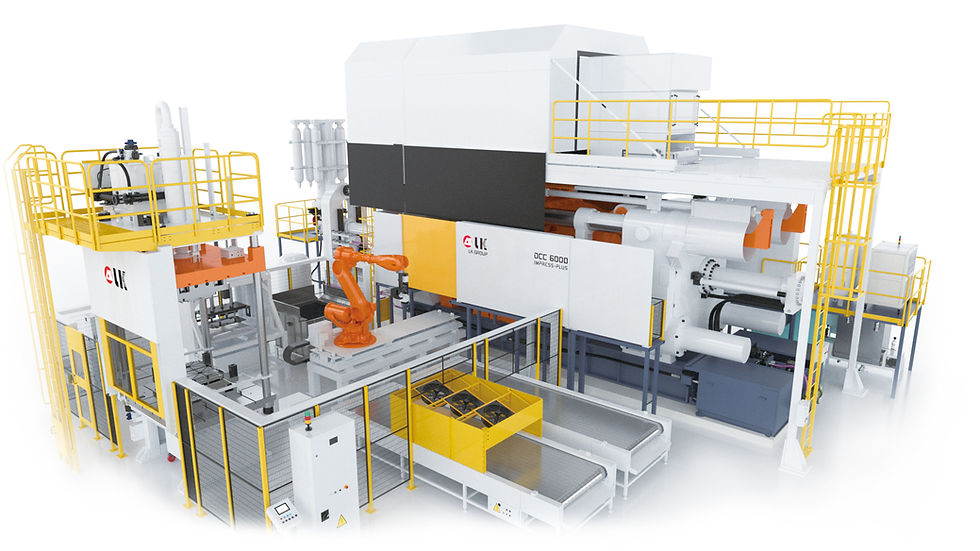
Latest Generation Pressure Castings Machines
Vair National Castings Company is setting up Various Types of Castings Technologies under the same room giving Potential Customer One Stop Solution.
Vair National Castings Company
VNCC plans to develop Hybrid Foundry , hence offering latest generation Heavy Duty Machines in HPDC and GDC. By Adding Lost foam technology to Manufacture Aluminum Castings , VNCC will be one of the handful companies in the world offering such variety of Production Set up.
​
​
WE ARE CUSTOMER FOCUSSED


High Pressure Die Castings Machines
-
Injection system is powerful, achieves 8m/s or above for injection speed.
-
Easy to use, with advanced control system including color LCD for direct control.
-
Energy saving, operating cost is low with high performance.
-
Flexibility is extensive with various options and peripherals.
-
Clamping Force: 1,300 kN- 90,000kN.
-
Injection unit: Tie-bar type or C-frame are both available.

Lost foam technology
Lost foam casting is a process used to create complex metal pieces and parts in which molten metal evaporates a foam mold being held still with sand. The process starts with a polystyrene foam as the mold material which can be carved, machined from a foam block, or created using a process similar to injection molding.
​
The latter process uses beads of polystyrene that are heated inside an aluminum die to expand and fill the die. A completed polystyrene foam mold is then covered with a ceramic refractory coating to create a barrier between the foam and the sand in which the foam mold sits. The small amount of waste gas created can escape into the sand.
​
There are many advantages to rapid prototype casting. There is a reduced cost and lead time to create a part. There is little to no machining needed and there is a high level of design freedom. Incredibly complex shapes can be created with various characteristics that are difficult to achieve with other methods. An example is parts with thin walls.
The finished metal parts have a nice surface finish. A large disadvantage can be the time it takes to create a CAD design as well as the level of expertise it requires. Part sizes are also limited to the size of the printing area in the machine creating them. The metals that finished parts can be created in is limited by metals with a lower melting point.
